Investment by Suez to support research into the recycling of MDF has been welcomed by the company carrying out trials into a process to remove wood fibres from the material.
But, further development of the project will need boardmakers to take up the process which is now being trialled in Chesterfield.
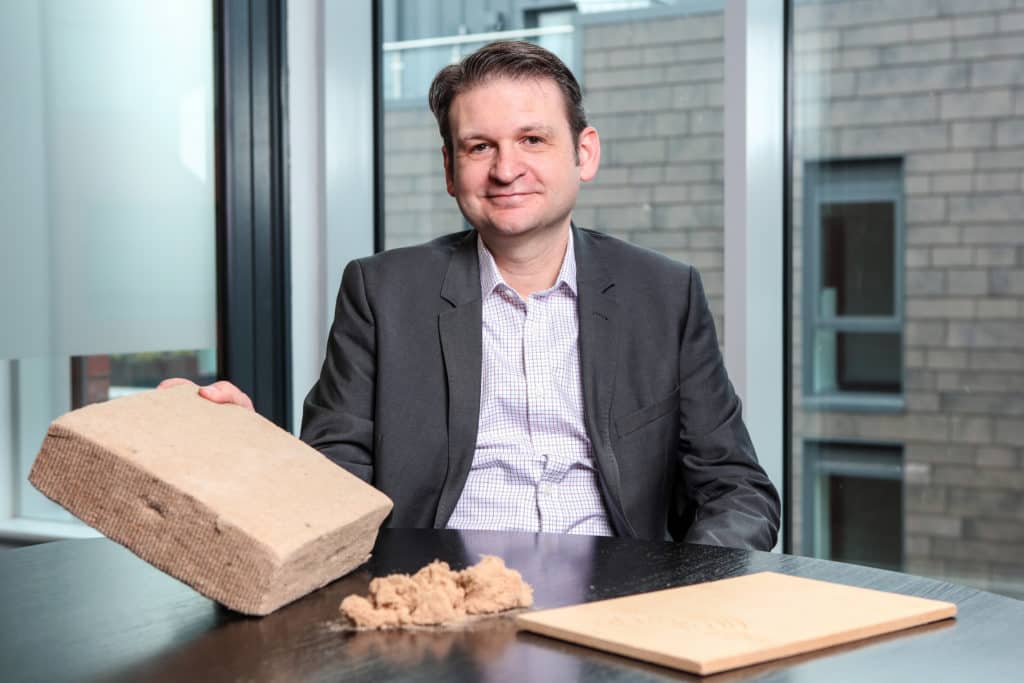
Furniture research expert Craig Bartlett who is leading the MDF project
MDF – medium density fibreboard – is a refined product with 950,000 tonnes of the material produced in the UK in 2015 for use in items such as drawer fronts, kitchen doors, skirting boards and furniture. Other boards include: OSB with bigger fibres used in roofing and flooring; and particle or chipboard with graded sizes of fibres and used in kitchen carcassing and flooring.
Investment
Suez announced earlier this month that it was putting £250,000 into the project. In what is akin to a ‘Dragon’s Den’ investment, the money will be used by MDF Recovery, the operations business of MDFR Natural Fibres Ltd of Anglesey.
MDF Recovery has been seeking investors for several years and has welcomed Suez’ support. Its research work has moved from initial studies at the University of Bangor’s biocomposites centre, under the supervision of Dr Rob Elias, to a trial facility which has now been set up in Chesterfield.
The managing director of MDF Recovery is Craig Bartlett who previously headed up research at FIRA, the Furniture Industry Research Association and has also been involved with work for resource charity WRAP. And, the project comes against a background where the wood panel manufacturing industry and FIRA have expressed concerns that too much wood generally is going for burning in biomass plants rather than firstly being recycled, or made available for furniture-making.
Commenting on the Suez investment in his company, Mr Bartlett said it would help the company’s quest “to commercialise the technology to make single-use MDF a thing of the past.”
He claimed that the recovered fibre “produced by the process is of the same high quality as fibre obtained from virgin wood and can be used as a direct substitute in the manufacturing process”.
Manufacturing
And, Mr Bartlett noted that the MDF Recovery technology can “be retro-fitted or designed into new plants and offers a robust solution for reworking waste and increasing yield at the MDF manufacturing plant”.

Fibres produced from earlier trials at Bangor University
Suez technical development director Stuart Hayward-Higham, said: “We are delighted to make this investment to continue assisting with the development of MDF Recovery’s ground-breaking technology. The technology should literally give a new prolonged shelf-life for MDF, one of the most popular materials across the construction and furniture industry from large scale commercial projects to the army of shelf-fitters and DIY carpenters up and down the country. Zero waste production for the wood component of MDF is now a real possibility.”
The investment is coming from the ‘waste products division’ of Suez in line with its “commitment to delivering practical, environmentally responsible and innovative waste management solutions”. It follows earlier work with MDF Recovery on an Innovate UK project linked to the trial plant.
MDF Recovery has said that its proposed recycling of the MDF wood fibres comes at a time when demand for virgin timber from many other sources is growing. Not only could the project mean that waste MDF from commercial sources – such as shopfitting – and from civic amenity sites could be recycled, but also offcuts from the MDF production process as well.
Biomass
Suez’ involvement is seen as the company trying both to add value to the business and also to help in meeting specifications for biomass; the company is a major player in supplying waste wood for biomass. MDF contains glues with short fibres and these can cause problems in biomass plants because the material easily fragments and can cause dust.
THE PROJECT:
Using a water based process an electrical heating stream is created which separates fibres within the MDF from the glues.
At the Chesterfield demonstration site, material is supplied by Suez and using a water based process an electrical heating stream is created which separates fibres within the MDF from the glues. This means that the fibres are liberated using heat and moisture and the MDF fibres swell back up, can then be dried and with a resin go back in to making fibreboard.
Now discussions are to continue with the board making sector. But, involvement is not expected quickly because the volumes needed to supply the board makers will take time to produce should the project eventually move from trial to real world stage. Another potential route for the material is into making insulation products as pictured.
Related links
MDF Recovery
The post Suez invests as MDF recycler seeks board sector support appeared first on letsrecycle.com.
Source: letsrecycle.com Waste Managment